IoT-Retrofitting
18.09.2019, 07:11 Uhr
Maschinen und Anlagen ins IoT katapultieren
Um fit fürs IIoT zu werden, sind in vielen Fällen keine Neuanschaffungen nötig. Oft lassen sich auch Bestandsmaschinen kostengünstig nach- beziehungsweise aufrüsten.
Umrüsten für das Industrielle Internet der Dinge (IIoT): Eine vollständige Vernetzung der Maschinen und Anlagen bildet die Grundlage für die Smart Factory, die Produktivitätssteigerungen, geringere Produktionskosten und eine bessere Ressourceneffizienz verspricht. Es kommt jedoch selten vor, dass Unternehmen dafür eine neue Fabrik errichten oder den kompletten Maschinenpark erneuern, denn dies wäre mit einem enormen Aufwand und unzumutbar hohen Kosten verbunden. Auch ist das meist gar nicht notwendig, weil viele Maschinen trotz eines vergleichsweise hohen Alters einwandfrei laufen. Deshalb rückt das IoT-Retrofitting immer mehr in den Fokus.
Damit ist das Nachrüsten bestehender Maschinen und Anlagen gemeint, um sie für die Industrie 4.0 fit zu machen. Dieser Strategie kommt im Zusammenhang mit Predictive Maintenance nach Beobachtung von Experten besondere Bedeutung zu, weil Unternehmen allein dadurch viele Kosten sparen können. Ein weiterer spannender Anwendungsbereich ist die Automatisierung der Steuerung. Dieser ist zwar deutlich kleiner, nicht zuletzt, weil Sicherheitsaspekte hier eine weitaus grössere Rolle spielen. Richtig umgesetzt kann der Ansatz jedoch ebenfalls viele Vorteile bieten: «Dadurch kann zum Beispiel eine kontinuierliche Fernsteuerung sichergestellt oder das Verhalten der Maschine bei auftretenden Fehlern bestimmt werden», erläutert Stefan Ried, IoT Practice Lead und Principal Analyst beim IT-Marktforschungs- und Beratungsunternehmen Crisp Research.
Neues Leben durch Sensoren
Das Ziel des IoT-Retrofittings ist vereinfacht gesagt das Abgreifen und Weiterleiten von Daten, die bis dato nicht zugänglich waren. Um dies zu ermöglichen, können die Maschinen und Anlagen im ersten Schritt mit Sensorik ausgestattet werden, um zum Beispiel Prozess- oder Maschinendaten abzulesen. Diese werden mit Hilfe von Kommunikationstechnik wie IoT-Gateways über das Netzwerk an die übergeordneten IT-Systeme zur Weiterverarbeitung weitergeleitet. Sollten die Anlagen und die Fabrikhallen über keine oder unzureichende Internetverbindung verfügen, muss ausserdem die entsprechende Konnektivität geschaffen werden. Anschliessend können Daten in einer zentralen Software, beispielsweise einer IoT-Plattform oder einem Manufacturing Execution System (MES), gesammelt und verarbeitet werden, um Ergebnisse zu visualisieren und Handlungsempfehlungen zu generieren.
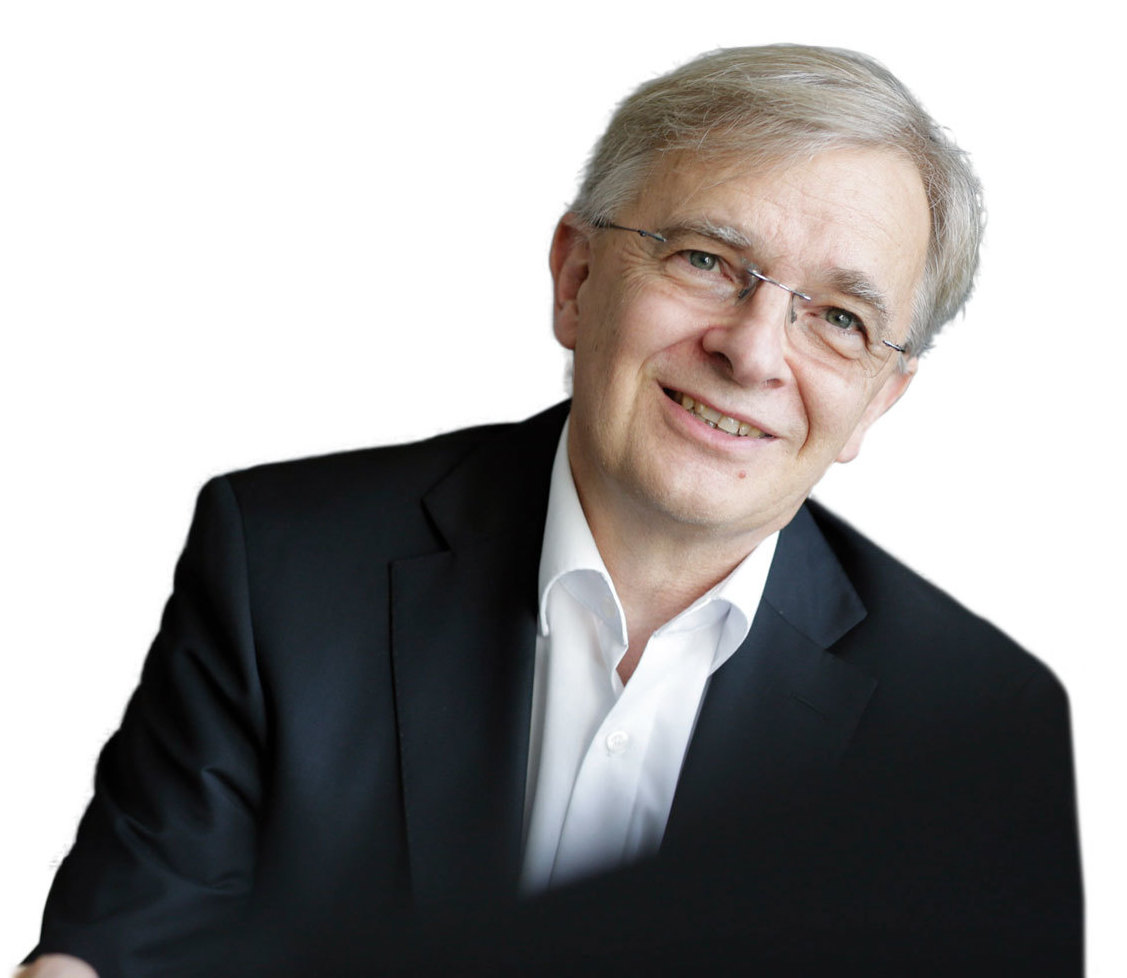
“Was auf dem Weg zum IoT alles möglich ist, kann vor dem ersten Schritt gar nicht überblickt werden„
Bernhard Müller, Geschäftsleitung Industrie 4.0 der SICK
Welche Hardware und Software im Endeffekt tatsächlich benötigt wird, hängt immer von der Frage ab, was der Zweck des IoT-Retrofittings ist und welche Daten für diesen Zweck verwendet werden sollen. «Wenn es zum Beispiel um Predictive Maintenance geht, dann ist die Maschine selbst der Informationsgeber. Bei der Überwachung von Prozessen wie Materialfluss oder Qualität werden Daten ausserhalb der Maschine erfasst», erklärt Bernhard Müller, Geschäftsleitung Industrie 4.0 beim Sensorhersteller SICK. Darüber hinaus muss geklärt werden, welche Voraussetzungen bereits erfüllt sind, denn manche Maschinen verfügen zwar über die erforderliche Sensorik, es fehlt aber zum Beispiel an einer Kommunikationsschnittstelle. Bei anderen müssen wiederum zusätzliche Sensoren angebracht werden.
Ein weiterer wichtiger Aspekt ist, dass Sensoren – ganz gleich ob vorhandene oder neu angebrachte – kontinuierlich enorme Datenmengen liefern. Davon ist jedoch womöglich nur ein kleiner Teil für die konkrete Maschine relevant, während der Rest zwar wichtige Einblicke hinsichtlich des gesamten Maschinenparks liefern kann, für die Performance-Überwachung dieser Maschine aber keine Rolle spielt.
Vor diesem Hintergrund werden die Themen Machine Learning und Edge-Computing für die Retrofit-Hardware immer relevanter. «Das Ziel ist, mehr Daten im Edge, sprich direkt im Sensor oder an der Maschine selbst, abzuarbeiten, sodass man nur noch die nützlichen Informationen in die Cloud legt», erklärt Bernhard Müller. So kann man beispielsweise nur ganz konkrete Parameter wie Geräusche oder Temperaturdaten von mehreren Maschinen in die Cloud senden, um diese dort auszuwerten und vorhersagen zu können, wann mit dem Ausfall einer der Maschinen zu rechnen ist.
Der neueste Trend geht also hin zu schlauerer Hardware für die Nachrüstung von Bestandsmaschinen. Das sieht auch Stefan Ried so: «Frühere Edge-Devices haben nur Daten von einem Gerät abgegriffen und einfach über das MQTT-Protokoll (Message Queuing Telemetry Transport) in die Cloud weitertransportiert. Heute besitzen sie jedoch sehr viel Logik, weil die Geräte leistungsstärker und die Algorithmen optimiert worden sind», ergänzt der Crisp-Research-Experte.